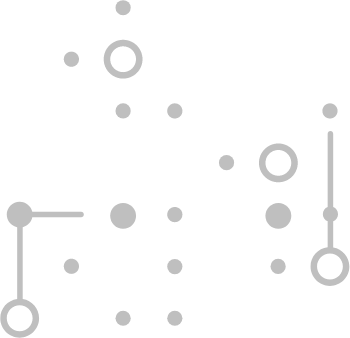
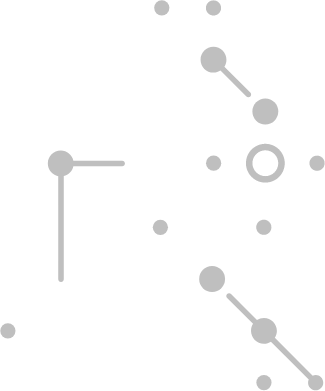
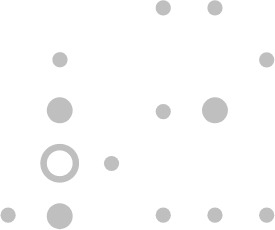
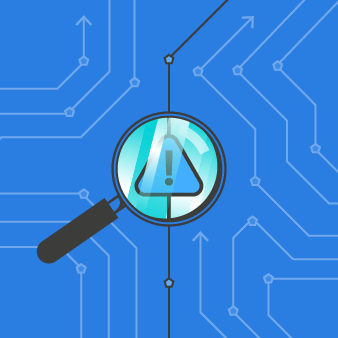
Maximise Uptime: Predictive Maintenance Tools, Benefits, and Real-World Examples
2025-03-19 13:03:09In the world of production lines, every minute counts. From food processing plants to automotive assembly lines, unplanned downtime quickly impacts your bottom line, reputation, and product quality. Take the example of automotive plants. According to research from Siemens, an hour's downtime in this sector costs more than $2 million. Among respondents, the average manufacturing facility suffers 20 downtime incidents a month and loses an average of 25 hours a month to unplanned downtime.
It doesn't take much thought to see how essential proper condition monitoring and predictive maintenance (PdM) are to counter this kind of loss.
However, although over 70% of Siemens respondents see PdM as a strategic priority, its actual level implementation in plants leaves much to be desired. This trend is visible in The State of Industrial Maintenance 2024, with most respondents using preventive and run-to-failure measures and only 30% reporting active use of PdM.
So, what are the obstacles to implementing predictive maintenance tools on a wider level in production facilities? And how can your company ease these to take advantage of PdM? Read on to find out!
Defining predictive maintenance
Predictive maintenance is a strategy that helps to maximise uptime by improving production asset reliability and scheduling equipment maintenance. It’s one of the essential features of Industry 4.0 and smart factory setups.
IoT and sensors deliver large volumes of data on nearly all aspects of production machinery and environment. Coupled with AI, IoT data can provide invaluable insights into operations, processes, and equipment conditions.
In production facilities, equipment reliability is paramount. Predictive maintenance tools help foresee possible performance issues by assessing machinery parameters and limits.
Various condition monitoring factors, such as sound (and ultrasound), vibration, temperature, and oil and fluid lubrication levels, enable the detection of anomalies and the avoidance of potential problems.
For instance, an increasing component temperature may indicate airflow blockage or wear. Abnormal vibration may indicate problems with moving parts. Changes in sound can provide early warnings of faults that the human ear cannot pick up.
Once processed and analysed, all this data enables more efficient automation of maintenance tasks, further reducing the need for human input. As a result, it can reduce equipment downtime by 30%—50% and increase machine life by 20%—40 %, as reported by McKinsey.
So, how do PdM solutions operate and help manufacturers keep equipment in good condition?
How do predictive maintenance tools work?
The basic answer is that they run on data. IoT sensors enable monitoring multiple machine data points and collecting data on your equipment’s temperature, vibration, humidity and other parameters.
Devices that production companies typically monitor include pumps, fans, compressors, motors, gearboxes, and bearings.
You can then create predictive models by analysing historical data and correlating it with previous equipment failures. Moreover, thanks to alerts, you can get notified of anomalies and act before they snowball into real issues.
As a result, you progress from reactive maintenance—fixing equipment when it goes down—to more proactive approaches, saving time and money and boosting performance.
While your overall equipment effectiveness (OEE) lingers at 50-75% in reactive and planned approaches, it can shoot up to 90% with predictive maintenance and more.
Let’s now consider how this increased equipment effectiveness translates into even more advantages for your production company.
Even more benefits of predictive maintenance tools
First, predictive maintenance tools reduce the risk of downtime. Equipped with real-time data on your machinery’s performance, they can help you stay on top of repairs by scheduling them in advance to avoid failures.
You can plan your repair tasks during non-critical periods and, if necessary, use spare equipment during maintenance to avoid downtime and maintain business continuity.
Secondly, PdM reduces unnecessary maintenance costs. Predictive maintenance tools allow you to start conservation and component replacement at a higher load or time than you’d expect within regular schedules. This process reduces expenses for new parts and saves time for your maintenance team.
Thirdly, PdM provides insights into the operation of integrated systems. With predictive maintenance tools, you can better understand the overall condition of complex systems in real-time.
Integrating data from all IoT devices allows you to analyse your entire business activity, spot the weakest links, and increase efficiency.
All these benefits stem directly from the ability to gather, store, and process large volumes of data—which wouldn’t be possible without the cloud.
Predictive maintenance tools in the AWS cloud
While all major cloud providers boast IoT solutions due to their scale and market penetration (31% in Q3 2024), AWS invariably holds the title of leader.
Here are some of the predictive maintenance tools and IoT services AWS currently offers:
#1: AWS IoT Greengrass
AWS IoT Greengrass supports you in building, managing, and implementing IoT software. More like an engine for software, it comes with integrations with S3, Cloudwatch, and Amazon Kinesys, allowing you to manage IoT devices quickly with AWS-integrated software.
You can install AWS IoT Greengrass client software on IoT devices and network them using the Hub to enable device communication. This feature lets you filter and aggregate data from sensors while allowing devices to act on the data they generate and run predictions based on ML models.
#2: AWS IoT Core
Integrated with AWS IoT Greengrass, this service facilitates managing IoT devices. By connecting millions of devices, you can monitor and manage them remotely.
It also supports the ability of devices to communicate with AWS services without the need to manage the infrastructure.
#3: AWS IoT Analytics
This tool automates the steps necessary to analyse data from IoT devices.
Once you collect data from AWS IoT Greengrass or external devices, you can start analysing it by running queries using the built-in SQL query engine. You can also perform more complex analyses with ML algorithms.
#4: Amazon SageMaker
This fully managed service involves the entire Machine Learning process for labelling and preparing data, selecting the algorithm, training the model, tuning and optimising it for deployment, making predictions, and taking appropriate action.
#5: Amazon Monitron
This system uses Machine Learning to detect anomalies in industrial equipment and enable predictive maintenance without requiring any technical knowledge of ML.
Amazon Monitron comes with wireless sensors for collecting input on vibrations and temperatures, a device that sends this data to AWS, and a mobile app for configuring IoT devices and receiving alerts about potential issues.
Its implementation is also straightforward. Simply attach a wireless device—the size of a safety matches box—to the machine, connect it to a gateway device via Bluetooth, and it will start sending data to the cloud via Wi-Fi.
As easy as it sounds, it only works on sensors from the Monitron service.
#6: Amazon Lookout for Equipment
Amazon Lookout for Equipment uses Machine Learning to detect anomalies in industrial equipment so you can take action and avoid unplanned downtime.
Once the service learns your equipment’s healthy state, it analyses the incoming sensor data in real-time and identifies signs that could lead to machine failure.
Unlike Amazon Monitron, Amazon Lookout gathers data from external sensors and historical records. Such data must remain in S3, Amazon’s object storage service. You can download it from there and move it for analysis in the Lookout for Equipment service.
Building an ML workflow for predictive maintenance tools
Building an ML model that captures the relationship between the normal features and your equipment’s degradation path helps estimate the time of potential failure and when to perform maintenance.
Typically, the steps necessary to build such a model involve the following:
#1 Data collection: get data from sensors.
#2 Prepare the data: clean the data by removing the noise and extracting useful features from raw data.
#3 Identify condition indicators: use extracted features to differentiate healthy operations from faulty conditions.
#4 Train the model: training the model using the extracted features helps detect anomalies and predict your equipment’s remaining service life.
#5 Deploy the model: implement and integrate the ML model for predictive maintenance in the cloud or on an edge device.
#6 Evaluate: assess the model using generated features.
That’s why typical ML workflows for predictive maintenance include multiple steps, intertwining data and technical expertise.
Despite the complex nature of PdM models, a growing number of companies across different industries use this strategy. Let’s now shift to some real-life examples of different predictive maintenance solutions.
Predictive maintenance tools in action
#1: Logistics & transportation
Predictive maintenance is critical in automotive and logistics because it helps to prevent sudden mechanical failures and reactive maintenance activities that disrupt operations.
By using ML to predict vehicle failures and schedule repairs, you can reduce downtime and repair costs.
You can build such a fleet management solution using the following tools from AWS:
#1 SageMaker Jumpstart is a Machine Learning hub that uses Amazon SageMaker and provides pre-trained, publicly available ML models for forecasting demand, detecting fraud, making custom recommendations, and analysing document data.
#2 Amazon S3 is a good choice for dataset storage.
#3 SageMaker Notebook is an ML compute instance running the Jupyter Notebook application, which is useful for model reprocessing, visualisation, and training.
#4 SageMaker endpoint is a place to deploy, view, and manage your model.
#5 AWS IoT Core enables uploading logs from sensors connected to your fleet vehicles.
#6 Amazon Kinesis Data Firehouse is a log storage for uploads to S3.
#7 AWS Lambda enables sending sensor logs to SageMaker to process and query the model for predictions.
#8 Amazon Aurora is a popular database that you can use to store your forecasts.
#9 Amazon QuickSight is a handy business intelligence tool for displaying collected results on a dashboard.
#10 Amazon SNS is a managed service that provides message delivery for notifications and alerts.
#11 Amazon Lookout for Equipment automatically analyses sensor data to detect equipment anomalies, diagnose issues, and prevent them without any ML experience.
Check this repository for more details on Amazon’s predictive maintenance solutions for fleet management.
#2: Energy & agriculture industries
Other great fields of application of predictive maintenance tools are energy, agriculture, and chemical markets.
Koch Ag & Energy Solutions is a global provider of value-added solutions for these fields. The company uses Amazon Monitron in its critical systems, using PdM tools to analyse data to prevent errors and reduce unplanned downtime.
The company had a big vision but started with a relatively small implementation and aimed to scale fast. Once the pilot proved the value, KAES proceeded with expanding the PdM solution to more machines, using the data to refine the business case and collaborate with stakeholders and partners.
You can watch the entire case study in this Re: Invent talk.
#3: Food and FMCG
Frito-Lay is a US subsidiary of PepsiCo that manufactures and sells crisps and multiple snack foods. Its Tennessee facilities produce over 150 million pounds of product per year, including household names like Ruffles, Cheetos, Doritos, and Fritos.
The company implemented a programme of predictive maintenance tools across its 50 most critical assets. The system uses remote vibration monitoring, analysing the data and alerting the plant operator in case of anomalies. It also takes advantage of IR analysis on electrical equipment, some rotating components, and heat exchangers.
Here are a few examples of Frito-Lay’s PdM system in action. First, vibration readings confirmed by ultrasound helped to prevent a PC combustion blower motor from failing and shutting down the whole potato chip department.
Second, thanks to detecting increased acid levels in oil samples from a baked extruder gearbox, the company was able to spot oil degradation and avoid shutting down its entire production unit.
#4: Rail industry
SMRT Trains Ltd is a Singaporean rail operator that maintains more than 282 kilometres of track and, on average, transports 2 million passengers daily.
Previously, the company relied on manual maintenance planning methods, but these were insufficient for assessing the whole network’s asset condition to improve commuter safety and convenience.
That’s when SMRT Trains implemented a Predictive Decision Support System (PDSS). The solution creates a repository designed specifically to centralise all the data and an analytics engine that transforms the input into maintenance strategy and resource optimisation recommendations.
Challenges in PdM deployments
Although the examples above may make PdM sound exciting, predictive maintenance tools aren’t suitable for every company – at least not immediately.
The amount of time, human resources, and financial investment necessary to successfully implement such solutions aren’t always cost-effective for all SMEs.
Therefore, before planning a PdM implementation, consider these factors:
#1: Your current infrastructure
Often, deploying predictive maintenance tools requires upgrading outdated technologies and integrating old systems with new ones. Monitoring systems can only collect data from devices capable of storing or sharing data.
Moreover, you’ll need to consider investing in data management tools and data communication infrastructure.
#2: Know-how
Implementing new predictive maintenance tools is one thing, but what’s even more important is getting your staff ready to use them.
Training your people to use new solutions and precisely interpret the data can be time-consuming and costly. However, that’s the only way to ensure a satisfying rate of PdM tool adoption – so you need to account for that, too.
#3: Data collection in place
For predictive maintenance to work effectively, the availability of large volumes of present and historical data is essential – ideally, with all prior failure or proxy data.
If your business doesn’t yet have such structure in place, the ROI of predictive maintenance tools will surely experience delays.
Therefore, before investing in PdM, it’s paramount that your organisation gathers, stores, and processes data adequately, or otherwise, you risk losing time and money.
Now is the best time to start preparing for predictive maintenance tools
As you can see, the potential of predictive maintenance tools is enormous, but their adoption is still in the infancy in many cases. While PdM promises significant savings, and improved production reliability, it comes with a price tag that may be too high for SMEs all at once.
That’s why your company needs to be smart about adopting predictive maintenance tools and mechanisms in the right order. If you wish to gain a competitive advantage, now is the best time to assess your data collection and infrastructure’s readiness for PdM.
The more production data you have, the better maintenance predictions and schedules you can create, so waste no time.
Contact us, and let’s talk about getting your business ready for predictive maintenance tools.