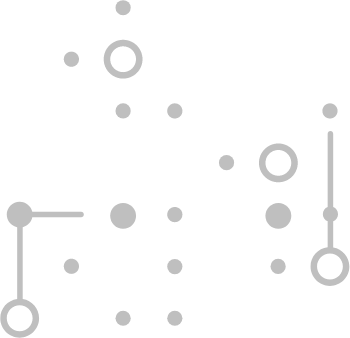
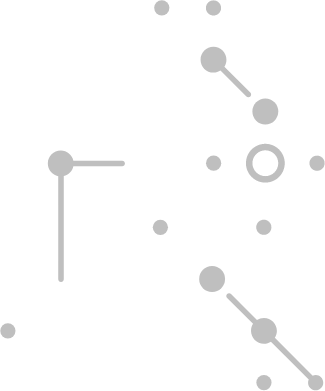
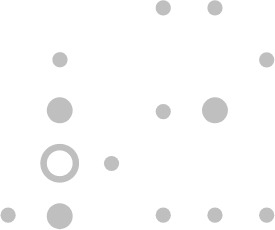
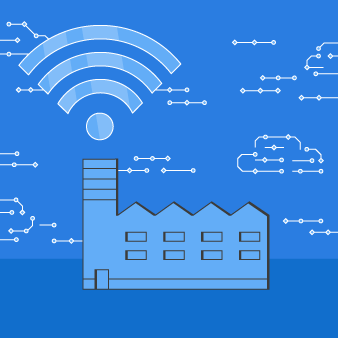
Smart Factory: How IT Infrastructures Pave the Way to Industry 4.0
2025-05-19 13:46:37In the age of ubiquitous intelligent wearables and appliances, it was only a matter of time before you'd hear about a smart factory. Even the most traditional industries, like manufacturing, are also yielding to digital transformation's potential. Don't be misled to think that it's a completely new concept, though. While Google Trends shows a growing interest in "Industry 4.0" since the 2010s, technology-driven transformation of manufacturing has been occurring at least since the 1970s.
In this article, I'll discuss the opportunities smart factory solutions offer manufacturers and outline the role of technologies such as AI, IoT, and the cloud. As not all that glitters is gold, I'll then discuss the challenges related to Industry 4.0 implementations—most notably implementation costs and security, especially for SMEs.
That's why manufacturers need to account for their organisational readiness for new tech, and the final part of this text discusses key steps to ensure success in that matter.
But first things first – let's start by clarifying core concepts:
What is a smart factory?
A smart factory is a highly automated manufacturing facility that optimises production processes using technologies such as AI, the Internet of Things, robotics, cloud computing, and advanced analytics.
These technologies enable manufacturers to unlock many benefits, from real-time monitoring to reducing downtime and improving product quality. This is possible thanks to interconnected machinery, equipment, and systems that communicate with each other almost without human interference.
However, despite their advanced appearance, digital solutions available to manufacturers today aren’t that new. Instead, they build on what’s been in place since the previous industrial revolution.
Industry 3.0 vs. Industry 4.0
Since 1960, computer networks, processes, and other IT solutions have been increasingly used to automate production lines and mechanisms.
Many processes central to the third industrial revolution already used logic processors and tech to enable automation and reduce the need for human interference.
Industry 4.0 took this approach to the next level, collecting large amounts of production floor data and using it to further reduce the need for human supervision.
Two key differentiators of Industry 4.0
Building on Industry 3.0 advancements, the fourth industrial revolution expands on already existing technologies by significantly increasing network connections and creating Digital Twins.
Digital Twins—virtual representations of physical objects—enable communication with other facilities and transmit information about production systems.
This development marks the next phase in automating production. However, what truly enables the smart factory is the networking of all manufacturing systems and the creation of cyber-physical production systems.
While the use of networking in production isn’t new, technologies like AI, IoT, and robotics help manufacturers take it to unprecedented levels. Seamless communication of systems, components, and people over the network enables nearly autonomous production and has vital consequences for factory design.
Smart factory blends the physical with the virtual
The increased integration of technologies enhances efficiency and flexibility in production processes, enabling quick adaptation to changing market conditions.
Machinery becomes increasingly autonomous, controlled, and managed by technologies that feed on real-time production data. As algorithms and software take control over physical hardware, the need for human operators further decreases.
Let’s consider a CNC machine as an example to better illustrate this paradigm shift. Previously, such a tool would run largely autonomously but still require input from a human operator and base its automation on human input and decisions rather than data.
Under the Industry 4.0 paradigm, the same CNC machine would follow set programming parameters but also use data to optimise operations without the need for human input.
A model example of a smart factory
The World Economic Forum named Agilent Waldbronn’s site a Global Lighthouse for Manufacturing Innovations. It is a stellar example of technologies driving dramatic improvements in factories.
Before implementing changes, this life-science producer struggled with supply chain disruption, changing product requirements, and fluctuations in demand.
By combining Industrial IoT (IIoT) and AI for rapid simulation and prediction, Agilent achieved dramatic improvements: a 35% increase in quality, a 44% productivity growth, and a 48% rise in output.
Predictive maintenance was one specific approach that boosted Agilent’s productivity—and here’s what you need to know about it.
Smart factory’s superpower
Predictive maintenance is a relatively recent approach that involves optimising production processes by increasing equipment lifespan and operational sustainability.
Predictive maintenance enables decreasing downtime, and production halts while reducing repair costs by predicting potential failures before they happen. According to SAP, predictive maintenance algorithms can reduce downtime by up to 50% and increase asset lifespan by 40%.
Despite the unquestionable value of predictive maintenance, manufacturers still need to reckon with considerable capital expenses, especially instrumentation, software, and expertise.
This disadvantage is pronounced in the early stages of predictive maintenance development. Getting the desired ROI is challenging when the actual data on equipment behaviour patterns is scarce and, in new systems, when operational knowledge is still low.
As a result, companies often defer investment in predictive maintenance, missing out on the opportunities it offers. While full-scale implementations are expensive, gradually deploying IoT sensors, actuators, and tags for critical assets can make a huge difference.
Collecting real-time data enables manufacturers to spot potential threats early and optimise maintenance schedules. But to make the most of that, you need some other technologies.
Smart factory’s enablers: cloud computing and AI/ML
Let’s get things straight: Industry 4.0 wouldn’t be possible without cloud computing’s power—a lot of it, as IoT sensors gather volumes of data from connected devices.
The cloud provides the infrastructure for storing, processing, and turning data into valuable insights into production efficiency and the performance of individual machines and equipment.
It’s cloud computing that enables AI and machine learning algorithms to be run to analyse and interpret production data. Without the cloud, you’d have zettabytes of information without insights for predictive maintenance or automated decision-making.
AI and ML let manufacturers use the wealth of operational data to increase visibility, predictability, and process automation.
By uncovering patterns and anomalies, systems powered by advanced analytics and AI algorithms enable predictive maintenance and automated production optimisation.
Generative AI takes this capability even further. For example, Gen AI solutions can interpret telemetry from smart factory equipment to reduce unplanned downtime, maximise utilisation, and suggest potential solutions and service plans.
The possibilities don’t end there, and so the march towards completely autonomous production continues – with one large caveat.
Smart factory and cybersecurity
As great as increasingly networked production systems and machinery sound, they come with one inherent challenge: cybersecurity.
With a low tolerance for downtime, servers full of data, and networks of costly equipment, manufacturers are attractive to ransomware gangs and other threat actors. The expanded attack surface of smart factories makes it challenging to detect and defend against these threats.
In 2023, manufacturing was the third-most affected industry in Arctic Wolf® Incident Response ransomware attacks and fourth-most represented in IR business email compromise engagements.
One essential type of attack in smart factory environments is Denial of Service (DoS), which makes systems unavailable. DoS can overwhelm servers with requests, crash processes with malformed input data, infiltrate viruses, or turn off sensors, disrupting normal operations.
A notable example of cybercrime aimed at this sector is the Stuxnet malware, which in 2009 brought entire manufacturing infrastructures to an abrupt halt.
More recently, Triton hit media headlines due to its detrimental abilities, specifically targeted at industrial control systems (ICS). Interfering with Safety Instrumented System (SIS) controllers, this malware allows attackers to destroy processes protected by these systems by feeding them false data.
Security best practices in smart factories
While a smart factory’s cybersecurity is a topic for a complete discussion, best practices in these environments should irrevocably include the following:
1. Identifying and fixing outdated systems, unpatched vulnerabilities, and poorly secured files;
2. Ensuring that technology suppliers and connected equipment manufacturers commit to regular security and software patches and audits;
3. Taking a security-first approach to the deployment of all new connected systems;
4. Constant monitoring of IoT devices and data flows is used.
You are only as safe as your network’s weakest link – and in manufacturing, this weakness or oversight can have costly consequences.
Other challenges on the SME’s way to the smart factory
As already signalled, implementing smart manufacturing can incur challenges that can be particularly hard for small to medium-sized enterprises (SMEs)
SMEs often face greater financial resources and knowledge limitations, making the digitisation process more challenging. They frequently lack the skills necessary to plan and implement new technologies, facing a mismatch between Industry 4.0 theories and their specific requirements in production, logistics, organisation, and more.
The interconnected nature of systems introduces significant risks for SMEs, especially when it comes to cybersecurity. An oversight on one layer of IoT architecture—sensors, network, service/data, and application layers—can potentially affect the entire IT infrastructure.
Moreover, manufacturing supply chain systems have inherent security vulnerabilities that attackers can exploit. One supplier susceptible to phishing attacks and theft of credentials can lead to massive data exposure, potentially affecting the entire organisational process.
When planning smart manufacturing solutions, SMEs need to account for access control, ideally through authentication mechanisms, cryptographic processes, and behavioural analysis.
That’s why manufacturing SMEs shouldn’t go it alone but choose a trusted technology partner for support in building the smart factory.
Structuring the path to smart factory success
Here’s a typical process you could expect when navigating the shift to smart manufacturing at your business:
1. Analyse your starting point
First, conduct a thorough assessment of your company’s current maturity in technology, processes, and team capabilities. Use that moment to spot specific areas that can benefit from adopting Industry 4.0.
2. Prioritise Industry 3.0
Ensure your company’s management buy-in, especially when it comes to securing commitment and support from management and key stakeholders. Inform the entire team of the planned changes and suggested process improvements.
Moreover, make strides to connect your OT (Operational Tech) and IT (Informational Tech) departments. Encourage their collaboration on implementing integrated production scheduling systems and other necessary Industry 3.0 technologies to see the first results and secure further support from your stakeholders.
3. Define your strategy and start small
Outline your desired goals and outcomes and establish a clear vision and target maturity level for your future adoption of Industry 4.0 solutions.
Create a detailed implementation plan laying out the steps, resources, and timeline. Identify potential roadblocks and plan how to address them.
Begin with small pilot projects addressing specific challenges where Industry 4.0 solutions deliver the most value for your company. Success in these first projects will help to build momentum for larger, more complex implementations.
4. Build a smart factory environment
Develop an ecosystem that allows physical and digital elements to communicate and promotes collaboration across different departments.
To get the desired ROI on your smart factory investment, you need to be ready technologically and culturally for the changes Industry 4.0 will bring to your company.
That’s why training and upskilling your teams on the new solutions shouldn’t be an afterthought but a central part of your digital transformation strategy.
5. Continue improving processes
Gather feedback from your team to continuously improve the smart factory implementation so that your new solutions deliver maximum value to the company.
Conclusion
Thanks to advancements like predictive maintenance, smart factory implementations can significantly reduce downtime, increase equipment life, and unlock new efficiencies.
Reaping these benefits is only possible with the cloud and AI/ML. These two technologies provide the basis for processing production floor data and using it to automate process optimisations.
Despite the unquestionable benefits of smart factory implementations, manufacturing companies often need help with related security threats, especially DoS attacks.
While the shift to smart manufacturing comes with even more challenges, thorough planning, pilot projects, and working with a trusted tech partner definitely make this process smoother.
Let’s discuss your company’s digital transformation needs. Contact us, and we’ll be happy to listen and advise.